Face to Face Magnetic Disc Couplers, Magnetic Torque Couplers, Hysteresis Face to Face Coupling,Hysteresis Magnetic Coupling, Magnetic Torque Couplers, Magnetic Synchronous Coupling
Original factory, accept visitors
Free design, technical support
Quality assurance, one year warranty
What are Magnetic Disc Couplers ?
Magnetic disc couplers provide a contactless means of torque transfer. They are predominantly utilized in pumps for applications requiring seal-less operation, thereby preventing the escape of corrosive, toxic, or flammable liquids into the atmosphere.
The concept is straightforward: Opposite poles attract. This fundamental principle enables the transmission of torque from one magnetic hub to another. By rotating one magnetic hub, the torque is magnetically conveyed to the companion hub. This transmission can occur through air or via a non-magnetic barrier like stainless steel or fiberglass, achieving complete isolation of the inner from the outer hub. The design excludes any contacting components.
Understanding magnetic disc couplers
Magnetic disc couplers are composed of two opposing discs that incorporate powerful rare earth magnets. Torque applied to one disc is conveyed across an air gap to the other disc. Thanks to their simple, flat design, these couplings can accommodate angular misalignment of up to 3 degrees or parallel misalignment of up to 1/4 inch while still transmitting a significant portion of the rotational torque. Moreover, an affordable flat barrier can be fabricated to separate the atmospheres or fluids surrounding the two discs.
Parameter
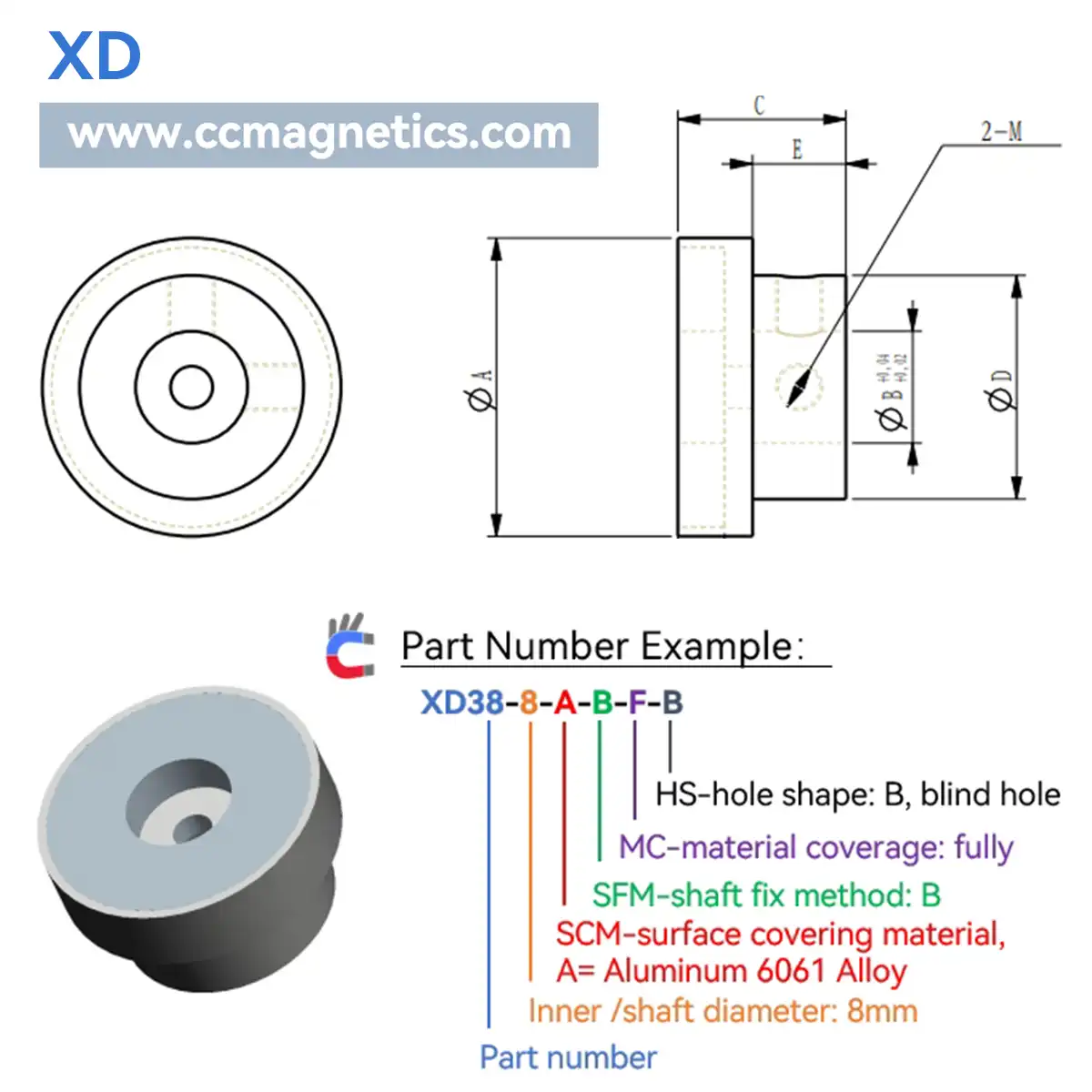
PN | B (in) | SCM | SFM | MC | HS | Max Speed RPM | Tq1 (in. lbs) | Tq5 (in. lbs) | A (in) | C (in) | D (in) | E (in) | M |
---|---|---|---|---|---|---|---|---|---|---|---|---|---|
XD12 | 0.16~0.24 | S/L | A | F | B/T | 35,500 | 0.4 | - | 0.47 | 0.63 | 0.47 | - | M3 |
XD24 | 0.24~0.39 | S/L/A | B/C/A | F/H | B/T | 35,000 | 3.7 | 0.4 | 0.94 | 0.71 | 0.71 | 0.39 | M4 |
XD28 | 0.24~0.39 | S/L/A | B/C/A | F/H | B/T | 34,000 | 6.6 | 1.1 | 1.1 | 0.71 | 0.79 | 0.39 | M4 |
XD32 | 0.31~0.47 | S/L/A | B/C/A | F/H | B/T | 32,000 | 17.3 | 2.8 | 1.26 | 0.71 | 0.94 | 0.39 | M5 |
XD38 | 0.31~0.59 | S/L/A | B/C/A | F/H | B/T | 30,000 | 26.4 | 7.3 | 1.5 | 0.71 | 1.1 | 0.39 | M5 |
XD43 | 0.47~0.79 | S/L/A | B/C/A | F | B/T | 26,500 | 33.6 | 10.6 | 1.69 | 0.79 | 1.18 | 0.47 | M5 |
XD50 | 0.47~0.79 | S/L/A | B/C/A | F | B/T | 23,000 | 37.2 | 13.3 | 1.97 | 0.87 | 1.34 | 0.51 | M5 |
XD63 | 0.59~0.98 | S/L/A | B/C | F | B/T | 20,000 | 97.4 | 39.8 | 2.48 | 0.98 | 1.42 | 0.59 | M5 |
XD68 | 0.59~0.98 | S/L/A | B/C | F | B/T | 17,500 | 143.4 | 69 | 2.68 | 1.18 | 1.57 | 0.71 | M5 |
XD90 | 0.79~1.38 | S/L/A | B/C | F | B/T | 13,500 | 201.8 | 77 | 3.54 | 1.5 | - | 0.79 | M6 |
XD78 | 0.71~1.18 | S/L/A | B/C | F | B/T | 15,000 | 163.7 | 88.5 | 3.07 | 1.26 | 1.65 | 0.71 | M5 |
XD100 | 0.79~1.38 | S/L/A | B/C | F | B/T | 12,000 | 252.2 | 92.9 | 3.94 | 1.57 | - | 0.87 | M6 |
XD120 | 1.1~1.5 | S/L/A | B/C | F | B/T | 10,000 | 292.1 | 108.9 | 4.72 | 1.97 | - | 1.18 | M8 |
XD130 | 1.38~1.57 | S/L/A | B/C | F | B/T | 9,000 | 442.5 | 173.5 | 5.12 | 1.77 | - | 0.98 | M8 |
PN | B (mm) | SCM | SFM | MC | HS | Max Speed RPM | Tq1 (N.m) | Tq5 (N.m) | A (mm) | C (mm) | D (mm) | E (mm) | M |
---|---|---|---|---|---|---|---|---|---|---|---|---|---|
XD12 | 4~6 | S/L | A | F | B/T | 35,500 | 0.05 | - | 12 | 16 | 12 | - | M3 |
XD24 | 6~10 | S/L/A | B/C/A | F/H | B/T | 35,000 | 0.42 | 0.04 | 24 | 18 | 18 | 10 | M4 |
XD28 | 6~10 | S/L/A | B/C/A | F/H | B/T | 34,000 | 0.75 | 0.12 | 28 | 18 | 20 | 10 | M4 |
XD32 | 8~12 | S/L/A | B/C/A | F/H | B/T | 32,000 | 1.95 | 0.32 | 32 | 18 | 24 | 10 | M5 |
XD38 | 8~15 | S/L/A | B/C/A | F/H | B/T | 30,000 | 2.98 | 0.82 | 38 | 18 | 28 | 10 | M5 |
XD43 | 12~20 | S/L/A | B/C/A | F | B/T | 26,500 | 3.8 | 1.2 | 43 | 20 | 30 | 12 | M5 |
XD50 | 12~20 | S/L/A | B/C/A | F | B/T | 23,000 | 4.2 | 1.5 | 50 | 22 | 34 | 13 | M5 |
XD63 | 15~25 | S/L/A | B/C | F | B/T | 20,000 | 11 | 4.5 | 63 | 25 | 36 | 15 | M5 |
XD68 | 15~25 | S/L/A | B/C | F | B/T | 17,500 | 16.2 | 7.8 | 68 | 30 | 40 | 18 | M5 |
XD78 | 18~30 | S/L/A | B/C | F | B/T | 15,000 | 18.5 | 10 | 78 | 32 | 42 | 18 | M5 |
XD90 | 20~35 | S/L/A | B/C | F | B/T | 13,500 | 22.8 | 8.7 | 90 | 38 | - | 20 | M6 |
XD100 | 20~35 | S/L/A | B/C | F | B/T | 12,000 | 28.5 | 10.5 | 100 | 40 | - | 22 | M6 |
XD120 | 28~38 | S/L/A | B/C | F | B/T | 10,000 | 33 | 12.3 | 120 | 50 | - | 30 | M8 |
XD130 | 35~40 | S/L/A | B/C | F | B/T | 9,000 | 50 | 19.6 | 130 | 45 | - | 25 | M8 |
Parameter Notes:
Term | Explanation | Notes |
---|---|---|
SCM | Surface Covering Material | A=Aluminum 6061 Alloy (UNS A96061), |
S=Stainless Steel 304 (UNS S30400), | ||
L=Stainless Steel 316 (UNS S31600), | ||
T=TC4 Titanium Alloy, Ti-6Al-4V, (UNS R56400). | ||
SFM | Shaft Fixing Method | A,B,C, refer to the picture for details. |
MC | Material Coverage | F= Fully, H= Half |
HS | Hole Shape | B= Blind hole, T=Through hole |
Tq1 | Torque, gap = 1mm / 0.03in | The torque value shown is for a 1mm or 0.03in gap. |
Tq5 | Torque, gap = 5mm / 0.2in | The torque value shown is for a 1mm or 0.03in gap. |
Advantages of Magnetic Disc Couplers
- Very low noise and vibration
- No wear No dust
- No heat generation
- Oil-free
- Power transmission through wall
- Torque limiter function
- Easy attaching and detaching
- Large tolerance for declination and eccentricity
Magnetic disc vs co-axial coupling comparison
Magnetic disc vs co-Axial coupling comparison |
![]() |
![]() |
---|---|---|
Coupling style | Magnetic disc couplings ( XD ) | Co-axial magnetic couplings ( XC ) |
Permanent-magnetic | √ | √ |
Contactless | √ | √ |
Maintenance-free | √ | √ |
Torsionally flexible | √ | √ |
Low vibrations | √ | √ |
Material | Standard: SS304. Options: Aluminum alloy 6061,Stainless steel 316L,PVC, available) |
Standard: SS304. Options: SS316/UNS S31603. |
Containment shroud | None | Optional |
Axial forces | High axial force which must be restrained | Coupling finds its own center with ~0 axial force |
Shaft fixing method | Small size type A, big size type B & C available |
Type B |
Slip torque adjustment | Air gap can be adjusted to increase or decrease slip torque |
Coupling hubs can be seperated axially to decrease slip torque (axial force will result) |
Angular misalignment capacity | 3° Max | Ensure coupling hubs (or barrier if used) do not contact |
Parallel misalignment capacity | 6.35mm (0.25in) Max | Ensure coupling hubs (or barrier if used) do not contact |
Containment barrier | Simple flat barrier | Top-hat shaped barrier |
Max. pressure resistance [bar] | Up to 80 bars depending on size | Up to 90 bars depending on size |
Max. temperature resistance [°C] | 150/300 depending on magnet material | 150/300 depending on magnet material |
awesomeava19 –
Good quality & quick delivery time.
stay1071 –
Great product.Very happy.Good quality.
protector3plus –
Received espectacular support during my ordering process. All questions and concerns, not matter how many were addressed in a professional matter. Very satisfied.